失效分析 | 揭秘产品失效背后的真相
设计缺陷
- 设计是产品性能和可靠性的源头,如果设计本身存在不足,就如同建造高楼没有稳固的地基。设计可能无法满足预期功能要求,例如一款手机在设计时对散热考虑不足,当长时间使用高能耗应用时,就容易因过热而出现死机、卡顿等失效现象。在工业领域,若功率模块设计时对散热结构考虑不充分,当模块高负荷运行时,产生的热量无法及时散发,就会导致芯片温度过高,性能下降甚至烧毁。
- 失效机理:以功率模块为例,由于散热路径设计不合理,热阻过大,热量无法有效传递到散热片。根据热传导公式:

当热阻增大,相同功率下芯片温度急剧上升,超过芯片的耐受温度,导致芯片内部的半导体材料特性发生变化,如载流子迁移率降低,进而使芯片的导通电阻增大,功耗进一步上升,形成恶性循环,最终烧毁芯片。
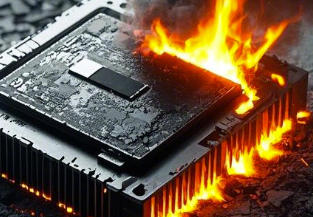
应力过载
- 产品都有其设计的承受极限,一旦在某些情况下承受超出其设计能力的应力负荷,就容易引发失效。像一辆额定载重为 5 吨的货车,若长期超载运输 8 吨甚至更重的货物,其发动机、轮胎等部件都会加速损坏,最终导致车辆无法正常运行。在新能源汽车领域,车辆在连续高速行驶、频繁急加速和急刹车时,电机和电池会承受较大的负荷,超出其设计工况,可能导致电池过热引发故障。
- 失效机理:新能源汽车电机过载时,电流会急剧增大。根据焦耳定律:
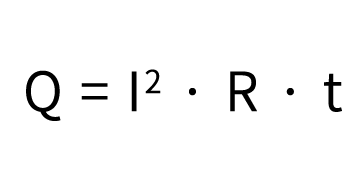
过大的电流会使电机绕组产生大量热量。同时,电机的反电动势会因转速变化而改变,导致电机内部磁场紊乱,进一步加剧能量损耗和发热。过高的温度会使电机绕组的绝缘材料性能下降,最终导致绝缘击穿,电机短路失效。对于电池而言,过载放电会使电池内部化学反应速率加快,产生大量气体,导致电池内部压力增大,可能引发电池鼓包甚至爆炸。
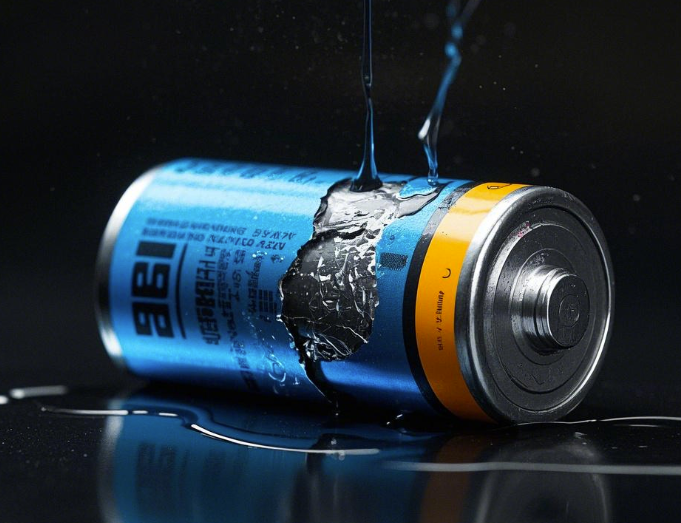
变异性影响
- 生产过程难以做到完全一致,这种变异性可能导致部分产品性能不稳定。在芯片制造过程中,哪怕是极其微小的工艺差异,都可能使芯片的性能出现波动,进而引发产品失效。在新能源汽车电池生产中,不同批次的电池材料和制造工艺的微小差异,可能使电池容量、内阻等参数不一致,影响电池组的整体性能。
- 失效机理:在电池生产中,活性物质的涂层厚度不一致是常见的变异性因素。根据电池容量公式:

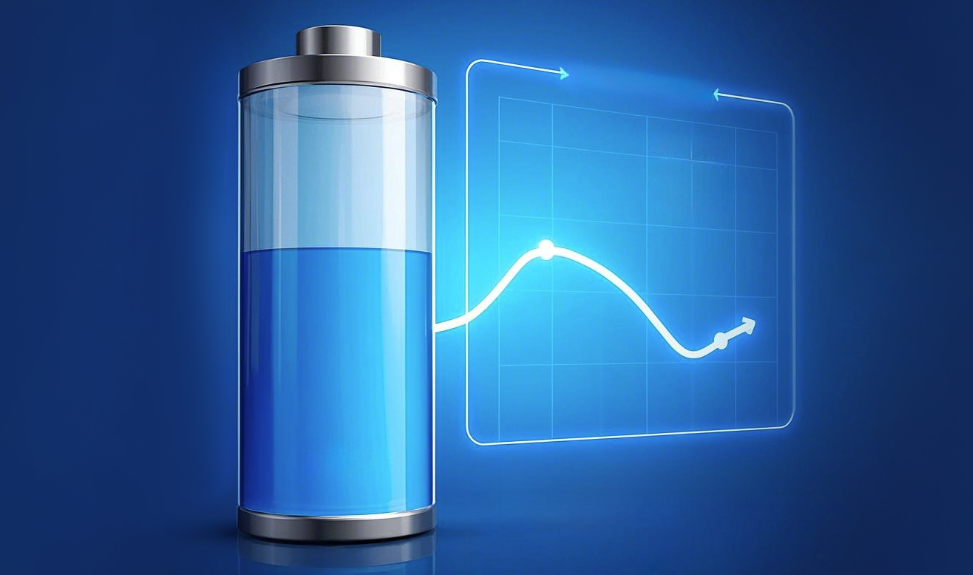
磨损老化
- 磨损引起的失效是指那些最初设计足够强壮的组件,由于长期使用而逐渐变弱并最终失效的过程。随着时间推移,材料和组件会因磨损而逐渐降低强度直至失去功能,如应力强度干涉模型,应力不变的情况下,材料本身的强度随时间降低。家中的水龙头,经过多年的频繁开合,内部的密封橡胶圈会逐渐磨损,导致漏水,这就是典型的磨损老化导致的失效。新能源汽车的电机电刷,在长期运行中会逐渐磨损,导致接触不良,影响电机输出功率。
- 失效机理:新能源汽车电机电刷与换向器长期摩擦,电刷表面的材料不断被磨损剥离。根据磨损理论:
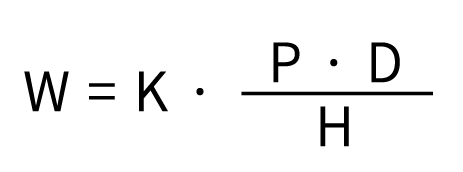
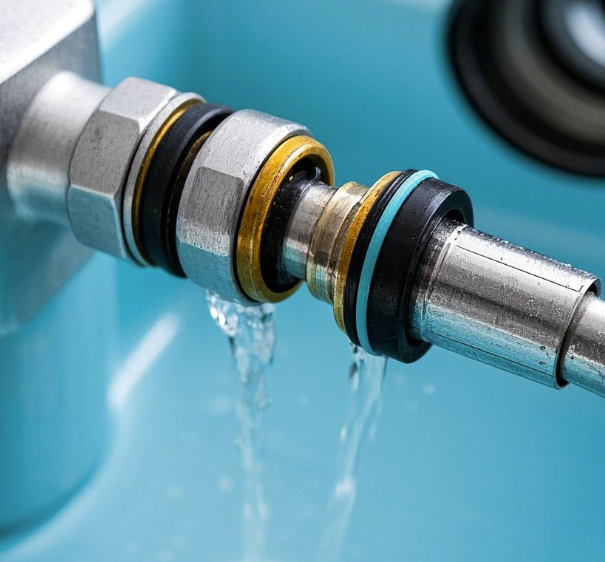
时间依赖性机制
- 时间依赖机制引起的失效,这类失效通常是由特定的外部条件或内部变化导致的,并且在一定时间内逐渐显现出来,腐蚀和疲劳是常见的例子。
- 失效机理:PCBA产品在潮湿环境下出现间歇性失效,根据电化学迁移模型:
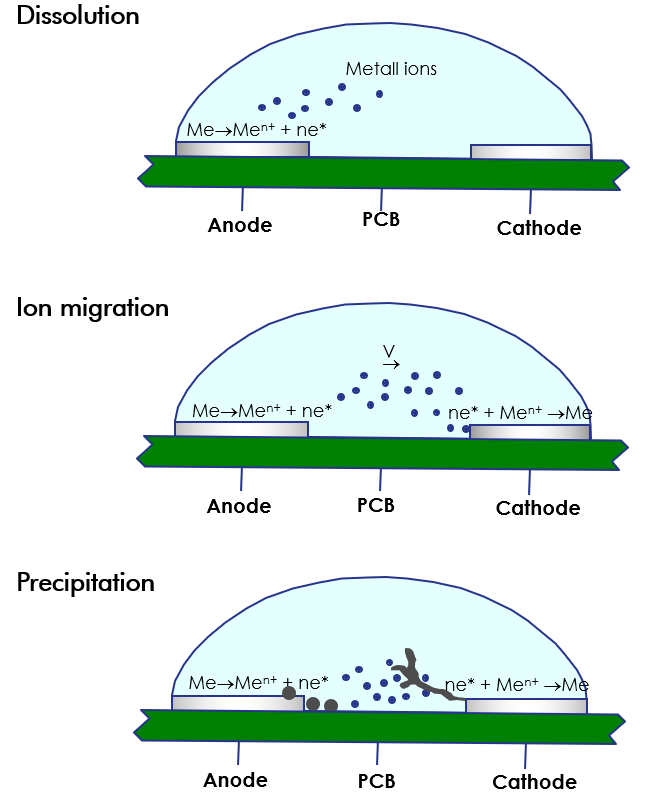
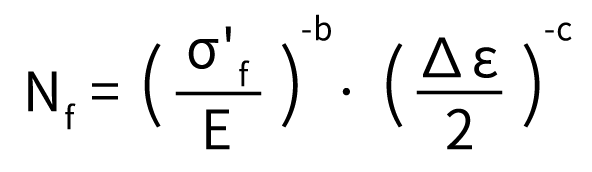
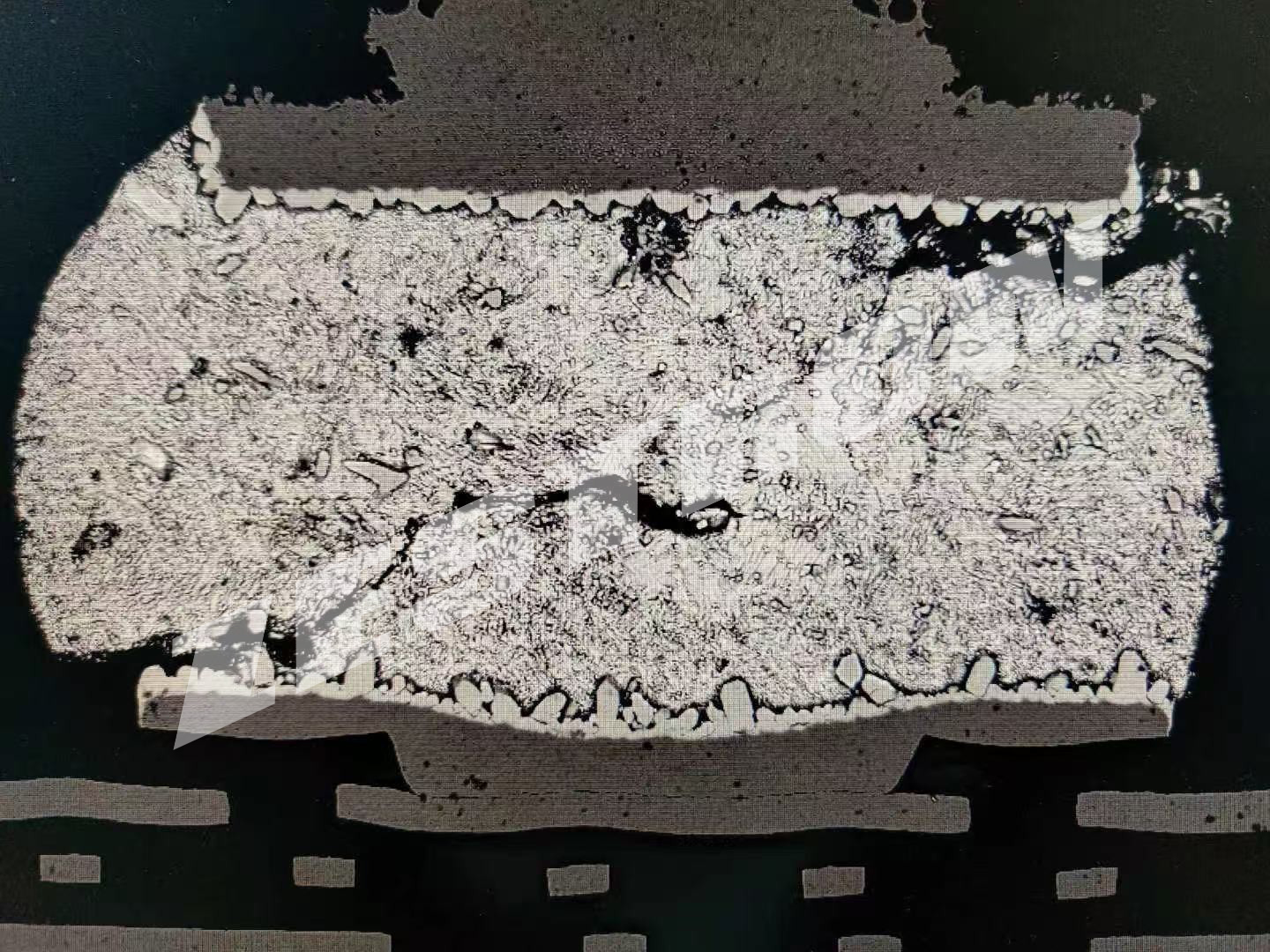
隐藏缺陷(Sneaks)
- 隐藏缺陷是那些不易被发现的设计或制造缺陷,但却可能引发意想不到的失效。
- 失效原因-虚焊问题:在 SMT 焊接的 PCBA 产品中,虚焊是一种常见的隐藏缺陷。虚焊可能是由于锡膏的质量问题、焊接温度不足等原因导致的。在正常工作时,虚焊的焊点可能不会表现出明显的问题,但在受到热冲击或机械振动时,虚焊的焊点会出现开裂,使电路连接中断。
人为错误
- 在设计、制造、安装或维护过程中,人为失误也是导致失效的重要原因之一。
- 失效原因-元器件错误贴装:在 SMT 生产线上,如果操作人员误将错误的元器件贴装到 PCBA 板上,会导致产品功能异常。例如,将电阻值错误的电阻贴装到电路中,会改变电路的工作参数,使产品无法正常工作。螺丝未按规定扭矩拧紧:在功率模块的安装过程中,如果安装人员没有按照规定的扭矩拧紧螺丝,会导致模块与散热片之间的接触不良。根据热阻公式:
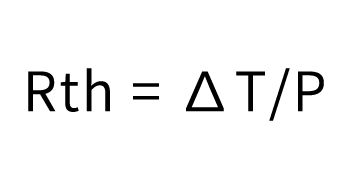
其他潜在因素
- 还有许多其他可能引起失效的原因,如环境条件和外部干扰等因素。